Outpacing the Competition: How Reusable Casts Are Redefining Orthopedic Care
- Samuele Molinaro
- Feb 24
- 3 min read
As the orthopedic industry evolves, many companies are striving to improve the comfort, ease, and functionality of casts, yet the disposable nature of many solutions remains a significant issue. Many new products are designed to be lightweight, breathable and easy to apply, offering superior comfort to patients compared to traditional plaster or fiberglass casts. However, despite the advancements in patient comfort, the environmental impact and costs of disposable products remain significant concerns.
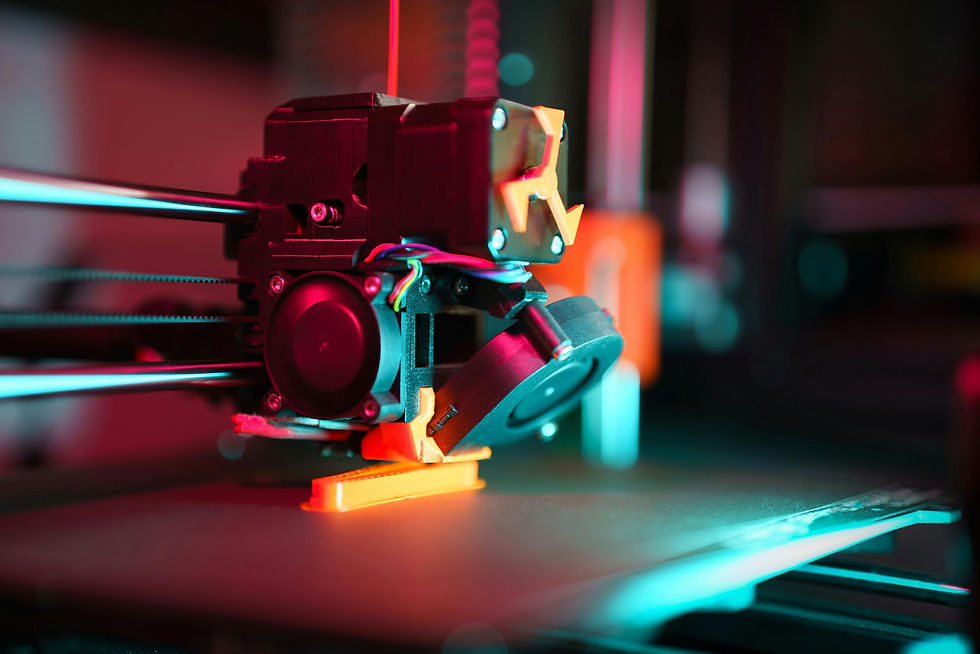
The biggest trend in the market includes 3D-printed casts, which offer a customized fit and enhanced patient comfort. These casts are typically designed to be waterproof, light and breathable, offering an alternative to the restrictive nature of traditional casts. However, 3D printing also brings its own set of challenges. Logistics and application time are some of the hurdles, with the need for scanning and printing adding complexity to the process. For each patient, an individual scan is required, leading to longer turnaround times and potential delays in treatment. The need for specialized equipment further increases the costs and changes in the patient’s condition, such as swelling or shrinkage, can render the cast ineffective, requiring new scans and additional printing.
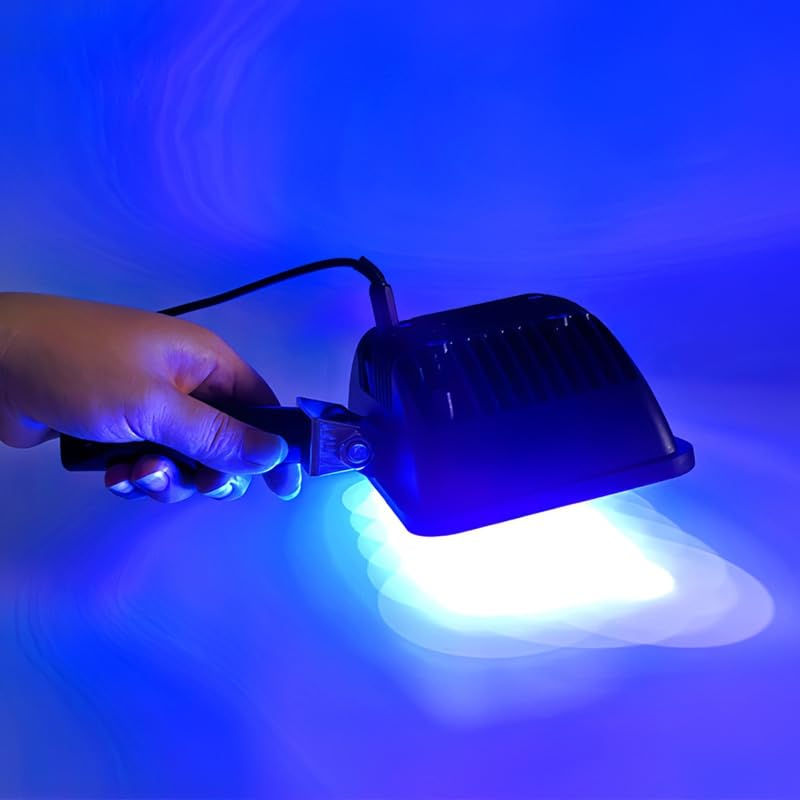
Other emerging technologies, such as light-cured resin casts and air-cured resin casts, seek to simplify the process. These options do not require scanning and can be applied more quickly. However, they come with their own disadvantages, such as the need for a custom UV light for light-cured casts or the need for a special curing liquid for air-cured casts. While they may offer advantages in speed and application, these solutions still present challenges in adjustability and remouldability, particularly as a patient’s fracture evolves during the healing process.
Amidst these innovations, a major area of concern is the environmental impact of medical waste. Many of these new casting solutions still rely on disposable materials, which continue to generate significant waste throughout the healthcare system. This presents a growing challenge as the medical field looks for more sustainable alternatives that minimize both waste and long-term costs.
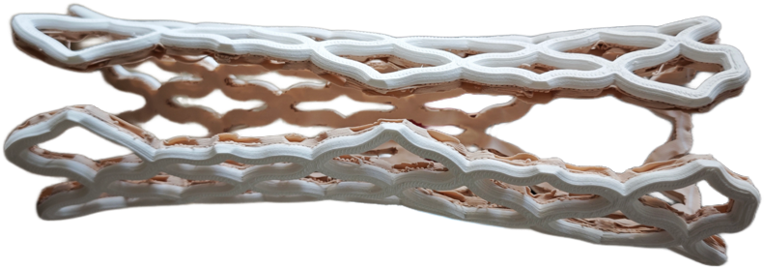
At the forefront of this shift is Castless, a company leading the charge in creating an eco-friendly, reusable orthopedic cast. Through the use of advanced 4D printing technology, Castless eliminates the need for disposable casts altogether, significantly reducing waste. 4D-printed casts are designed to be self-moulding, waterproof and comfortable, providing superior patient comfort and convenience compared to traditional solutions. Their self-moulding feature ensures that the cast fits precisely to the patient’s body, improving accuracy and eliminating the need for multiple tools and lengthy application processes. The result is a more efficient and sustainable casting solution, benefiting both patients and healthcare providers.
In addition to their comfort and environmental benefits, Castless’s reusable casts also offer significant cost savings for hospitals and healthcare providers. By reducing the need for disposable materials, Castless not only cuts down on waste management costs but also improves efficiency in the hospital setting, reducing application time and enhancing patient turnover.
With these advantages, Castless is positioning itself to be the leader in the orthopedic industry’s sustainable future, offering a solution that improves patient recovery, reduces waste, and enhances overall operational efficiency. The company is spearheading a paradigm shift in how orthopedic care is delivered, bringing sustainability and patient comfort to the forefront of healthcare innovation.
Comments